Un ghid cuprinzător despre cum să configurați o unealtă de tăiere cu strung
Configurarea unei scule de tăiere cu strung este o abilitate fundamentală pentru orice mașinist, mai ales atunci când are de-a face cu mașini de strunjire cu control numeric computerizat (CNC). Setarea corectă a sculei este crucială pentru obținerea unor rezultate de prelucrare precise și precise. În acest ghid cuprinzător, vom aprofunda în detaliile complicate despre cum să configurați o unealtă de tăiere cu strung pentru strunjirea CNC. De la elementele de bază ale componentelor sculelor de strung până la tehnici avansate de optimizare a performanței de tăiere, acest articol își propune să ofere o înțelegere cuprinzătoare a procesului. Până la sfârșitul acestui ghid, veți avea cunoștințele și abilitățile necesare pentru a configura o unealtă de tăiere cu strung cu încredere și precizie, asigurând rezultate optime în operațiunile dvs. de strunjire CNC.
Înțelegerea sculelor de tăiere cu strung
În lumea prelucrării, sculele de tăiere cu strung sunt componente indispensabile pentru modelarea și transformarea materiilor prime în piese proiectate cu precizie. Indiferent dacă lucrați cu strunguri manuale tradiționale sau cu mașini de strunjire CNC avansate, este esențial să aveți o înțelegere aprofundată a sculelor de tăiere cu strung. În această secțiune, vom aprofunda caracteristicile, funcțiile și tipurile de scule de tăiere cu strung.
Caracteristicile sculelor de tăiere cu strung
Uneltele de tăiere cu strung sunt proiectate pentru a efectua o varietate de operațiuni de prelucrare, cum ar fi strunjirea, fațarea, canelarea, filetarea și multe altele. Aceste instrumente au câteva caracteristici comune:
- Duritate: Uneltele de tăiere cu strung sunt de obicei fabricate din oțel de mare viteză (HSS), carbură sau alte materiale specializate pentru scule. Aceste materiale sunt alese pentru duritatea lor, permițând sculei să reziste la temperaturile și presiunile ridicate generate în timpul tăierii.
- Ultima generație: Muchia tăietoare a unei scule de strung este porțiunea care îndepărtează efectiv materialul din piesa de prelucrat. Este proiectat pentru a fi ascuțit și precis, iar geometria muchiei de tăiere poate varia în funcție de sarcina specifică pentru care este destinată unealta.
- Coadă: Tija sculei de strung este piesa care este prinsă în suportul sculei. Oferă stabilitate și rigiditate sculei în timpul proces de prelucrare. Designul tijei poate diferi în funcție de tipul de sculă și de specificațiile producătorului.
- Suport de scule: Suportul de scule este o componentă esențială, în special în strunjirea CNC, deoarece ține în siguranță unealta de strung în poziție. Trebuie să ofere stabilitate, precizie și ușurință de reglare pentru a asigura performanța optimă a sculei.
- Geometrie: Geometria sculei de tăiere, inclusiv unghiul de greblare, unghiul de degajare și spargerea așchiilor, joacă un rol semnificativ în determinarea performanței sculei. Geometria adecvată este esențială pentru a obține o îndepărtare eficientă a materialului și evacuarea așchiilor.
- Strat: Multe scule de tăiere cu strung vin cu acoperiri specializate, cum ar fi TiN (nitrură de titan) sau TiAlN (nitrură de titan și aluminiu), pentru a îmbunătăți durata de viață a sculei, a reduce frecarea și a îmbunătăți performanța.
Funcțiile sculelor de tăiere cu strung
Sculele de tăiere cu strung îndeplinesc câteva funcții fundamentale în procesul de prelucrare:
- Îndepărtarea materialului: Funcția principală a sculelor de tăiere cu strung este de a îndepărta materialul dintr-o piesă de prelucrat. Această îndepărtare poate avea loc prin strunjire (rotirea piesei de prelucrat în timpul tăierii), acoperire (crearea unei suprafețe plane) sau alte operații.
- Control dimensional: Uneltele de tăiere sunt responsabile pentru a se asigura că dimensiunile piesei prelucrate corespund specificațiilor dorite. Controlul precis este esențial pentru obținerea unor rezultate precise și consecvente.
- Finisaj suprafata: Calitatea finisajului suprafeței este determinată de claritatea sculei de tăiere, geometria și parametrii de tăiere utilizați. Un instrument de tăiere bine întreținut și configurat corespunzător contribuie la un finisaj neted și fin al suprafeței.
- Control cip: Controlul eficient al așchiilor este esențial pentru prevenirea acumulării de așchii și pentru menținerea unui mediu de lucru curat și sigur. Spărgătorul de așchii de pe unele unelte ajută la îndepărtarea așchiilor.
- Eficiență: Uneltele de tăiere cu strung sunt concepute pentru a face procesele de prelucrare eficiente și rentabile. Acestea ajută la minimizarea risipei de materiale și la optimizarea duratei de viață a sculei, reducând costurile de producție.
Tipuri de scule de tăiat strung
Uneltele de tăiere cu strung sunt disponibile într-o varietate de tipuri, fiecare adaptată la sarcini specifice de prelucrare. Iată câteva tipuri comune:
- Scule de strunjire: Aceste scule sunt versatile și utilizate pentru operațiuni de strunjire cilindrice. Ele pot modela suprafețele exterioare și interioare ale unei piese de prelucrat.
- Instrumente de alezat: Uneltele de alezat sunt folosite pentru a mari sau a finisa gaurile existente. Sunt proiectate pentru precizie și acuratețe în prelucrarea găurilor.
- Instrumente de despărțire: Uneltele de separare sunt folosite pentru a separa o piesă de prelucrat de un stoc mai mare. Ele creează linii de despărțire definite cu deșeuri minime.
- Instrumente de filetare: Uneltele de filetare sunt folosite pentru tăierea firelor pe o piesa de prelucrat. Ele vin în diferite forme și dimensiuni pentru diferite cerințe de filetare.
- Instrumente de canelare: Uneltele de canelare creează caneluri sau adâncituri pe o piesa de prelucrat, de obicei pentru a găzdui inele O, inele de reținere sau alte caracteristici.
- Instrumente de confruntare: Instrumentele de confruntare sunt concepute pentru a crea suprafețe plane la capătul unei piese de prelucrat. Ele sunt adesea folosite pentru a realiza suprafețe perpendiculare sau pentru a îndepărta materialul de la capătul piesei de prelucrat.
Înțelegerea caracteristicilor și funcțiilor uneltelor de tăiere cu strung este esențială pentru selectarea sculei potrivite pentru o anumită sarcină de prelucrare. Alegerea sculei de tăiere poate avea un impact semnificativ asupra calității și eficienței procesului de prelucrare, făcându-l o decizie critică în orice operație de strung. În plus, întreținerea adecvată și configurarea sculelor sunt vitale pentru a asigura rezultate consistente și precise, care vor fi discutate în detaliu mai târziu în acest ghid.
Tipuri de scule de tăiat strung
Sculele de tăiere cu strung sunt de diferite tipuri, fiecare proiectat special pentru o anumită sarcină de prelucrare. Înțelegerea acestor diferite tipuri de scule de tăiere și a aplicațiilor lor este esențială pentru selectarea instrumentului potrivit pentru o anumită lucrare. Iată câteva tipuri comune de scule de tăiere cu strung:
Scule de strunjire:
- Instrument cu nas rotund: Folosit pentru operațiuni de strunjire de uz general. Are o margine de tăiere rotunjită și este potrivită atât pentru tăieturi de degroșare, cât și pentru finisare.
- Instrument cu diamant: Numit după tăișul său în formă de diamant, este ideal pentru prelucrarea precisă pe diverse materiale, inclusiv metale și materiale plastice.
- Instrument cu nas pătrat: Prezintă o muchie de tăiere pătrată și este utilizată în mod obișnuit pentru operațiunile de răsucire a umărului și a umărului.
Instrumente de alezat:Bară de alezat internă: Folosit pentru a mări și finisa găurile existente într-o piesă de prelucrat. Este proiectat pentru precizie și poate crea dimensiuni interne precise.
Instrumente de despărțire:Lama de despărțire: Aceste unelte sunt folosite pentru a tăia o piesă de prelucrat dintr-un stoc mai mare. Ele creează o linie de despărțire definită cu deșeuri minime.
Instrumente de filetare:
- Instrument de tăiere a firului: Proiectat pentru a crea filete externe pe o piesa de prelucrat. Ele vin în diferite forme și dimensiuni pentru diferite cerințe de filetare.
- Instrument de urmărire a firelor: Folosit pentru urmărirea sau restaurarea firelor existente. Aceste instrumente sunt utilizate în mod obișnuit pentru repararea firelor.
Instrumente de canelare:Instrument de canelare: Aceste unelte creează caneluri sau adâncituri pe o piesa de prelucrat, adesea pentru a găzdui inele O, inele de reținere sau alte caracteristici.
Instrumente de confruntare:Instrument de confruntare: Folosit pentru a crea suprafețe plane la capătul unei piese de prelucrat. Este adesea folosit pentru a realiza suprafețe perpendiculare sau pentru a îndepărta materialul de la capătul piesei de prelucrat.
Instrumente de despărțire și canelare:Instrument combinat: Aceste unelte versatile sunt proiectate atât pentru operațiuni de despicare, cât și de canelare, economisind timp și schimbări de scule.
Instrumente de filetare și canelare:Instrument combinat de filetare și canelare: Ideal pentru lucrări care necesită atât operații de filetare, cât și de canelare pe aceeași piesă de prelucrat.
Instrumente de teșire:Instrument de teșire: Folosit pentru a crea teșituri sau margini teșite pe piesa de prelucrat. Teșiturile sunt adesea aplicate pentru a îmbunătăți aspectul și ușurința de asamblare a pieselor prelucrate.
Instrumente de moletare:Instrument de moletare: Moletarea este un proces de creare a unui model texturat pe o piesa de prelucrat, de obicei pentru o aderență sau o estetică îmbunătățită. Uneltele de moletare vin în diferite modele și modele.
Instrumente de formare:Instrument pentru formulare: Aceste instrumente sunt proiectate personalizat pentru geometrii specifice ale pieselor, adesea folosite pentru producerea de forme complexe și nestandard.
Instrumente de specialitate:Instrumente de profil: Folosit pentru crearea de profile complexe pe o piesa de prelucrat.
Instrumente de fațare și strunjire: Acestea sunt proiectate atât pentru operațiuni de fațare, cât și pentru operațiuni de strunjire.
Instrumente de tăiere: Proiectat pentru tăierea piesei de prelucrat pentru a crea piese separate sau pentru a elimina excesul de material.
Alegerea sculei de tăiere potrivite depinde de factori precum materialul prelucrat, finisajul dorit, dimensiunile necesare și operația specifică efectuată. Este esențial să alegeți unealta adecvată și să o întrețineți corespunzător pentru a asigura o prelucrare eficientă și precisă. Selectarea corectă a sculei, împreună cu configurarea și reglarea corectă, este crucială pentru obținerea unor rezultate de înaltă calitate în operațiunile de strung.
Componentele unei scule de tăiere cu strung
O unealtă de tăiere cu strung este un instrument de precizie conceput pentru modelarea, tăierea și îndepărtarea materialului dintr-o piesă de prelucrat. Pentru a înțelege cum funcționează și cum să o configurați corect, este esențial să vă familiarizați cu diferitele sale componente. Iată componentele cheie ale unei scule de tăiere cu strung:
- Suport de scule:Suportul pentru scule este partea care fixează unealta de tăiere în loc. Se atașează la stâlpul sculei strungului și oferă rigiditatea și stabilitatea necesare pentru operațiile de prelucrare. Suporturile de scule vin în diferite modele pentru a găzdui diferite tipuri de unelte de tăiere.
- Coadă:Tija este partea sculei de tăiere care se potrivește în suportul sculei. Este de obicei cilindric și este prins ferm în suport. Dimensiunile și forma tijei pot varia în funcție de tipul și designul sculei.
- Ultima generație:Muchia de tăiere este porțiunea ascuțită a sculei care contactează și îndepărtează materialul din piesa de prelucrat. Calitatea muchiei de tăiere și geometria acesteia afectează semnificativ performanța de tăiere și finisarea suprafeței. Este esențial să mențineți claritatea și precizia muchiei de tăiere.
- Introduce:Multe unelte de tăiere moderne folosesc inserții înlocuibile, care sunt de obicei realizate din materiale dure, cum ar fi carbura sau ceramica. Aceste inserții au geometria de tăiere și sunt fixate într-un buzunar de pe unealta de tăiere. Ele pot fi rotite sau înlocuite atunci când sunt uzate sau deteriorate, prelungind durata de viață a sculei.
- Nasul instrumentului:Nasul sculei este chiar vârful sculei de tăiere unde muchia de tăiere și insertul (dacă este folosit) se unesc. Botul sculei trebuie să fie poziționat și aliniat cu precizie pentru o prelucrare precisă. Unele scule de tăiere cu strung au o rază reglabilă a vârfului sculei pentru un control mai bun asupra performanței sculei.
- Flancul sculei:Flancul sculei este suprafața laterală a sculei de tăiere care nu face parte din muchia de tăiere. Unghiurile de joc adecvate pe flancul sculei asigură evacuarea așchiilor și reduc frecarea dintre sculă și piesa de prelucrat.
- Face grebla instrument:Fața greblă este suprafața sculei de tăiere care se află în fața piesei de prelucrat. Unghiul și starea feței greblei afectează formarea așchiilor și eficiența procesului de tăiere. Unghiul de greblare este un aspect critic al geometriei sculei.
- Unghiul sculei de relief:Unghiul de relief este unghiul dintre flancul sculei și axa sculei. Acesta asigură că muchia de tăiere nu se freacă de piesa de prelucrat, reducând frecarea și generarea de căldură.
- Unghi de degajare a sculei:Unghiul de degajare este unghiul dintre suprafața greblei și suprafața piesei de prelucrat. Permite așchiilor să curgă fără probleme și previne interferența între unealtă și piesa de prelucrat.
- Spărgător de așchii (dacă este cazul):Unele unelte de tăiere, în special cele utilizate pentru operațiunile de degroșare, au un spargetor de așchii, o canelură sau o crestătură pe fața greblei. Spărgătorul de așchii ajută la controlul formării așchiilor și la îmbunătățirea evacuării așchiilor.
Asamblarea, alinierea și întreținerea corespunzătoare a acestor componente sunt esențiale pentru realizarea unei prelucrari precise și eficiente. Alegerea sculei de tăiere și configurația acesteia trebuie să fie adaptate operațiunii specifice de prelucrare și materialului pe care se lucrează. Inspecția și întreținerea regulată a componentelor sculei de tăiere sunt, de asemenea, necesare pentru a asigura rezultate consistente și de înaltă calitate.
Alegerea instrumentului de tăiere potrivit pentru lucrare
Selectarea sculei de tăiere potrivite este o decizie critică în orice operație de prelucrare, deoarece influențează foarte mult calitatea, eficiența și precizia lucrării. Ar trebui luați în considerare mai mulți factori atunci când alegeți unealta de tăiere adecvată pentru o anumită lucrare. Iată un ghid despre cum să alegeți unealta de tăiere potrivită pentru proiectul dvs. de prelucrare:
1. Materialul piesei de prelucrat:
Materialul pe care îl prelucrați este unul dintre cei mai critici factori în alegerea sculelor. Diferitele materiale au duritate, conductivitate termică și abrazive diferite. Luați în considerare următoarele:
- Duritate: Materialele dure, cum ar fi oțelul întărit sau ceramica, necesită unelte de tăiere cu muchii de tăiere dure, cum ar fi inserțiile din carbură, pentru a rezista la forțele mari de tăiere.
- Materiale moi: Pentru materiale mai moi, cum ar fi aluminiul sau materialele plastice, oțelul de mare viteză (HSS) sau alte materiale pentru scule pot fi suficiente.
2. Operație de prelucrare:
Operația specifică pe care o efectuați, cum ar fi strunjirea, frezarea, găurirea, filetarea sau canelura, va dicta tipul de unealtă de tăiere de care aveți nevoie. Diferite instrumente sunt concepute pentru diverse sarcini, iar alegerea celei potrivite asigură performanțe optime.
3. Viteza de tăiere și viteza de avans:
Determinați viteza de tăiere și viteza de avans necesare pe baza materialului și a operației de prelucrare. Producătorii de scule de tăiere oferă recomandări pentru acești parametri pe baza designului sculei și a materialului prelucrat. Respectarea acestor recomandări este crucială pentru obținerea rezultatelor dorite.
4. Geometria sculei:
Luați în considerare geometria sculei de tăiere, inclusiv unghiul de greblare, unghiul de degajare și raza vârfului sculei. Geometria sculei trebuie să se potrivească cu materialul și tipul de tăiere. De exemplu, un unghi de greblare pozitiv este potrivit pentru materiale mai moi, în timp ce un unghi de greblare negativ este mai bun pentru materialele mai dure.
5. Dimensiuni piese de prelucrat:
Mărimea și dimensiunile piesei de prelucrat influențează și alegerea sculei. Unele unelte de tăiere sunt mai potrivite pentru operațiunile de degroșare pentru a îndepărta rapid materialul în vrac, în timp ce altele sunt proiectate pentru finisare pentru a obține dimensiuni și finisaje precise ale suprafeței.
6. Cerințe pentru finisarea suprafeței:
Dacă aveți nevoie de un finisaj specific al suprafeței, selectați o unealtă de tăiere cu geometria și claritatea corespunzătoare. Uneltele de finisare sunt proiectate pentru a oferi un finisaj mai neted al suprafeței, în timp ce sculele de degroșare sunt mai eficiente pentru îndepărtarea materialului.
7. Materialul sculei:
Alegerea materialului instrumentului este crucială. Uneltele din carbură, din oțel de mare viteză (HSS), ceramică și acoperite au toate avantajele și limitările lor. Luați în considerare factori precum durata de viață a sculei, rezistența la uzură și costul materialului sculei în decizia dvs.
8. Lichid de răcire și lubrifiere:
Luați în considerare dacă operațiunea de tăiere necesită lichid de răcire sau lubrifiere. Unele materiale generează căldură excesivă în timpul prelucrării, iar utilizarea lichidului de răcire sau a lubrifiantului potrivit poate prelungi durata de viață a sculei și poate îmbunătăți performanța de tăiere.
9. Acoperiri pentru scule:
Multe scule de tăiere moderne vin cu acoperiri specializate precum TiN (nitrură de titan) sau TiAlN (nitrură de titan și aluminiu) pentru a îmbunătăți rezistența la uzură și a reduce frecarea. Alegeți un instrument cu un strat adecvat pentru aplicația dumneavoastră specifică.
10. Considerații privind costurile:
Este esențială echilibrarea costului sculei de tăiere cu performanța și longevitatea acesteia. În timp ce uneltele premium pot oferi o durată de viață mai lungă și o performanță mai bună, este esențial să găsiți un echilibru care să se alinieze bugetului proiectului dumneavoastră.
11. Compatibilitatea suportului de scule și mașinii:
Asigurați-vă că unealta de tăiere aleasă este compatibilă cu sistemul de suport pentru scule al strungului sau al centrului de prelucrare. Suportul sculei trebuie să ofere stabilitate și rigiditate sculei de tăiere în timpul procesului de prelucrare.
În cele din urmă, unealta de tăiere potrivită pentru lucrare va depinde de o combinație a acestor factori. Consultați întotdeauna recomandările producătorului de scule și luați în considerare solicitarea de sfaturi de la mașiniști experimentați sau experți în scule dacă nu sunteți sigur. Selectarea și configurarea corectă a sculelor sunt fundamentale pentru obținerea unor rezultate de prelucrare eficiente și precise.
Configurarea instrumentului de tăiere cu strung
Configurarea unei scule de tăiere cu strung pentru strunjirea CNC este un proces sistematic care implică câțiva pași cruciali. Fiecare pas este vital pentru a se asigura că unealta de tăiere este poziționată și aliniată corect, conducând în cele din urmă la prelucrare precisă și eficientă. Să parcurgem procesul pas cu pas:
Pasul 1: Pregătirea strungului și piesei de prelucrat
Înainte de a putea configura unealta de tăiere, este esențial să pregătiți atât strungul, cât și piesa de prelucrat:
- Asigurați piesa de prelucrat: Asigurați-vă că piesa de prelucrat este bine fixată în mandrina sau mandrina de strung. Asigurați-vă că se rotește fără probleme, fără nicio clătinare sau vibrație.
- Siguranță: Asigurați-vă că sunt aplicate toate măsurile de siguranță, inclusiv utilizarea echipamentului individual de protecție (EIP) adecvat și setările corecte ale strungului.
Pasul 2: Selectarea suportului corect de scule
Suportul de scule este o componentă critică în procesul de configurare. Alegeți suportul de sculă adecvat pe baza unor factori precum tipul de unealtă de tăiere, operația care se efectuează și sistemul de stâlp de scule al strungului.
- Potriviți suportul pentru scule cu instrumentul de tăiere: Asigurați-vă că suportul pentru unelte este compatibil cu tipul și dimensiunea sculei de tăiere pe care intenționați să o utilizați.
- Rigiditatea suportului sculei: Alegeți un suport de scule care oferă stabilitate și rigiditate. Acest lucru este deosebit de important în aplicațiile de înaltă precizie.
Pasul 3: Montarea sculei de tăiere
Montarea sculei de tăiere presupune fixarea acesteia în suportul sculei și asigurarea că este poziționată ferm și corect:
- Asigurați instrumentul de tăiere: Introduceți unealta de tăiere în suportul pentru scule și strângeți toate mecanismele de prindere, cum ar fi șuruburi de fixare sau colțuri. Asigurați-vă că instrumentul este ținut în siguranță.
- Orientare: Verificați dacă unealta de tăiere este orientată corect în raport cu piesa de prelucrat. Unealta trebuie să fie poziționată pentru a cupla piesa de prelucrat la unghiul și adâncimea dorite.
Pasul 4: Reglarea înălțimii sculei și alinierii liniei centrale
Înălțimea corectă a sculei și alinierea liniei centrale sunt cruciale pentru obținerea unor dimensiuni precise de prelucrare:
- Reglarea înălțimii sculei: Reglați înălțimea sculei pentru a o alinia cu linia centrală a arborelui strungului. Utilizați un indicator de înălțime a sculei sau o bară de testare pentru a seta unealta la înălțimea corectă.
- Alinierea liniei centrale: Asigurați-vă că unealta este aliniată cu linia centrală a arborelui strungului. Nealinierea poate duce la prelucrare decentrată, afectând precizia piesei.
Pasul 5: Setarea compensării razei nasului instrumentului
Pentru strunjirea CNC, compensarea razei sculei ține cont de geometria sculei de tăiere. Acest lucru este deosebit de important atunci când utilizați instrumente de inserție:
- Determinați raza nasului sculei: Măsurați sau căutați raza exactă a nasului inserției sculei de tăiere pe care o utilizați.
- Introduceți valoarea razei: În software-ul de control CNC, introduceți valoarea măsurată a razei sculei pentru a vă asigura că mașina compensează geometria sculei la prelucrare.
Pasul 6: Setarea compensațiilor instrumentului
Decalajele sculei țin cont de variațiile dimensiunilor sculei și ale geometriei piesei de prelucrat. Acestea asigură că poziția sculei este reglată cu precizie pentru prelucrare:
- Selectați decalajul corect al sculei: Determinați valoarea corespunzătoare a decalajului sculei pe baza geometriei sculei și a operației de prelucrare. Această valoare de compensare compensează orice discrepanțe.
- Introduceți valori de compensare: Introduceți valorile de offset alese în software-ul de control CNC. Aceste valori vor instrui mașina despre cum să ajusteze cu precizie poziția sculei.
Pe tot parcursul procesului de configurare a sculei, utilizați instrumente de măsurare de precizie, cum ar fi micrometre, indicatori de înălțime și indicatori cadran pentru a verifica și a regla fin alinierea sculei. Inspectați și întrețineți în mod regulat unealta de tăiere pentru a vă asigura că rămâne ascuțită și în stare bună, deoarece o unealtă bine întreținută contribuie la rezultate de prelucrare consistente și precise.
Configurarea corectă a sculei de tăiere cu strung în acești pași este crucială pentru obținerea unor rezultate optime în operațiunile de strunjire CNC. Precizia și atenția la detalii în timpul instalării sculei sunt factori cheie în producerea pieselor prelucrate de înaltă calitate.
Optimizarea parametrilor de tăiere pentru strunjirea CNC
Optimizarea parametrilor de tăiere este esențială pentru realizarea operațiunilor de strunjire CNC eficiente și de înaltă calitate. Cele patru aspecte cheie de luat în considerare la optimizarea parametrilor de așchiere sunt vitezele și avansurile, adâncimea de tăiere, fluidele și lubrifianții de așchiere și gestionarea duratei de viață a sculei.
1. Viteze și avansuri:
- A. Viteza de taiere (viteza suprafetei):Viteza de tăiere, denumită adesea viteza de suprafață, este viteza la care interacționează piesa de prelucrat și unealta de tăiere. Se măsoară în picioare de suprafață pe minut (SFM) sau metri pe minut (m/min). Pentru a optimiza viteza de tăiere, luați în considerare materialul prelucrat și materialul sculei. Uneltele din oțel de mare viteză (HSS) au viteze de așchiere recomandate mai mici decât uneltele din carbură, de exemplu. Consultați datele producătorului de scule sau manualele de prelucrare pentru a determina vitezele de așchiere recomandate pentru anumite materiale și scule.
- b. Rata de hranire:Viteza de avans este viteza liniară cu care instrumentul de tăiere avansează în piesa de prelucrat. Se măsoară în inci pe rotație (IPR) sau în milimetri pe rotație (mm/rev). Pentru a optimiza viteza de avans, luați în considerare factori precum proprietățile materialului, geometria sculei și finisarea dorită a suprafeței. Vitezele de avans mai mari sunt în general mai productive, dar pot necesita unelte mai robuste.
- c. Relația între viteza de tăiere și viteza de avans:Echilibrarea vitezei de tăiere și a vitezei de avans este crucială pentru îndepărtarea eficientă a materialului. O creștere a vitezei de tăiere permite de obicei o viteză de avans mai mare, dar cele două trebuie ajustate împreună pentru a preveni uzura și supraîncălzirea sculei.
2. Adâncimea de tăiere:
- A. Adâncimea de tăiere (DOC):Adâncimea de tăiere este distanța la care instrumentul de tăiere pătrunde în piesa de prelucrat. Este esențial să luați în considerare capacitățile materialului și ale sculei. Optimizați adâncimea de tăiere în funcție de duritatea materialului și de rezistența și rigiditatea sculei. Tăieri superficiale pot fi necesare pentru materialele mai dure, în timp ce tăieturile mai adânci pot fi realizate în materiale mai moi.
- b. Adâncimea de tăiere axială și radială:La strunjirea CNC, luați în considerare atât adâncimea de tăiere axială (de-a lungul lungimii piesei de prelucrat) cât și radială (pe diametrul piesei de prelucrat). Adâncimile optime pentru fiecare va varia în funcție de operațiune și material.
3. Fluide de tăiere și lubrifianți:
- A. Alegerea fluidului de tăiere potrivit:Fluidele de tăiere sunt esențiale pentru disiparea căldurii, reducerea frecării și îmbunătățirea evacuării așchiilor. Alegeți fluidul de tăiere adecvat în funcție de material și operația de prelucrare. Pentru diferite materiale pot fi preferați lichidul de răcire solubil în apă, pe bază de ulei mineral sau sintetic.
- b. Aplicație adecvată:Aplicați fluide de tăiere în mod eficient în zona de tăiere pentru a asigura o lubrifiere și răcire adecvate. Acest lucru se poate face prin răcire prin inundație, sisteme de ceață sau prin livrarea lichidului de răcire prin scule, în funcție de capacitățile mașinii.
- c. Monitorizare și întreținere:Monitorizați în mod regulat nivelurile lichidului de tăiere, starea și contaminarea pentru a vă asigura că rămân eficiente. Mențineți sistemele de fluid de tăiere pentru a preveni probleme precum creșterea și degradarea bacteriilor.
4. Managementul duratei de viață a sculei:
- A. Inspecția și întreținerea sculelor:Implementați un program de rutină de inspecție și întreținere a sculelor pentru a vă asigura că sculele sunt în stare bună. Uneltele tocite sau deteriorate pot duce la o calitate slabă a prelucrării și la reducerea duratei de viață a sculei.
- b. Program de înlocuire a sculei:Stabiliți un program de înlocuire a sculelor bazat pe factori precum uzura sculei, timpul de funcționare al mașinii și cerințele de producție. Acest lucru ajută la prevenirea defecțiunilor neașteptate ale sculei și la menținerea unei calități constante a prelucrării.
- c. Optimizarea duratei de viață a sculei:Unele materiale și acoperiri pentru scule oferă o durată de viață mai lungă a sculei. Luați în considerare utilizarea sculelor de înaltă performanță pentru a optimiza durata de viață a sculei și pentru a reduce timpul de nefuncționare a producției.
- d. Controlul cipului de scule:Controlul eficient al așchiilor, inclusiv utilizarea spargetoarelor de așchii și geometria corectă a sculei, poate prelungi durata de viață a sculei prin reducerea uzurii induse de așchii.
Optimizarea parametrilor de tăiere în strunjirea CNC este un proces continuu. Experimentarea și reglarea fină pot fi necesare pentru a găsi cei mai buni parametri pentru o anumită aplicație. Monitorizați și ajustați în mod regulat acești parametri pentru a asigura performanța optimă de prelucrare, durata de viață a sculei și calitatea piesei. Parametrii de tăiere optimizați în mod corespunzător nu numai că îmbunătățesc eficiența prelucrarii, ci și reduc uzura sculelor și, în cele din urmă, costurile de producție.
Depanarea problemelor frecvente în setarea instrumentului
Depanarea problemelor comune în setarea sculelor este o abilitate esențială pentru mașiniști și operatorii CNC. Înțelegerea și abordarea acestor probleme poate ajuta la menținerea preciziei și calității operațiilor de prelucrare. Iată câteva probleme comune de setare a instrumentelor și soluțiile acestora:
1. Chatter instrument:
Problema: Fragmentarea sculei apare atunci când unealta de tăiere vibrează în timpul procesului de prelucrare, ceea ce duce la o finisare slabă a suprafeței, la uzura sculei și la deteriorarea potențială a piesei de prelucrat.
Soluţie:
- Reduceți viteza sau creșteți avansul: Reglați parametrii de tăiere fie prin scăderea vitezei de tăiere, fie prin creșterea vitezei de avans. Această schimbare poate atenua vibrațiile și poate reduce vibrațiile.
- Verificați rigiditatea sculei: Asigurați-vă că suportul pentru scule și unealta sunt fixate corect și că unealta nu se extinde prea departe de suport.
- Verificați prinderea piesei de prelucrat: Asigurați-vă că piesa de prelucrat este bine fixată pentru a preveni orice vibrații legate de piesa de prelucrat.
- Utilizați tehnici de amortizare: Unele mașini vin cu caracteristici pentru amortizarea vibrațiilor. Dacă sunt disponibile, luați în considerare utilizarea acestora.
- Alegeți un instrument mai rigid: Un instrument mai rigid, cum ar fi unul cu mai puține flute, poate ajuta la reducerea zgomotului.
2. Finisaj slab al suprafeței:
Problema: Un finisaj slab al suprafeței poate rezulta din probleme cu configurarea sculei sau parametrii de tăiere, ceea ce duce la suprafețe aspre sau inconsistente pe piesa de prelucrat.
Soluţie:
- Verificați geometria instrumentului: Asigurați-vă că geometria sculei de tăiere este adecvată pentru operațiune. O unealtă ascuțită cu geometria corectă este crucială pentru obținerea unui finisaj bun al suprafeței.
- Optimizați parametrii de tăiere: Reglați viteza de tăiere, viteza de avans și adâncimea de tăiere pentru a găsi cea mai bună combinație pentru materialul și operațiunea specifice.
- Verificați uzura sculei: Inspectați unealta pentru semne de uzură sau deteriorare, cum ar fi marginile ciobite. Înlocuiți sau șlefuiți din nou unealta după cum este necesar.
- Utilizați lichid de tăiere adecvat: Ungerea și răcirea corespunzătoare pot afecta în mod semnificativ finisarea suprafeței. Utilizați fluidul de tăiere potrivit pentru material și operațiune.
- Minimizați vibrațiile: Rezolvați problemele legate de vibrații pentru a evita crearea de nereguli la suprafață.
3. Inexactități dimensionale:
Problema: Piesele pot avea dimensiuni incorecte din cauza sculelor nealiniate sau a uzurii sculelor.
Soluţie:
- Verificați setarea instrumentului: Verificați dacă unealta este reglată corect, cu înălțimea și alinierea corecte în raport cu piesa de prelucrat.
- Calibrați mașina: Asigurați-vă că mașina CNC este calibrată corect și că interpretează cu acuratețe decalajele și datele sculei.
- Ajustați decalajele sculei: Corectați orice erori în decalajele sculei prin măsurarea precisă a sculei și introducerea valorilor de decalaj adecvate în controlul CNC.
- Inspectați uzura sculei: Inspectați regulat instrumentul de tăiere pentru uzură și înlocuiți-l sau șlefuiți-l atunci când este necesar.
4. Probleme de control al cipurilor:
Problema: Controlul necorespunzător al așchiilor poate duce la probleme cum ar fi înfundarea așchiilor, evacuarea slabă a așchiilor și deteriorarea piesei de prelucrat sau a sculei.
Soluţie:
- Alegeți geometria instrumentului potrivit: Selectați o unealtă de tăiere cu ruptorul de așchii sau geometria adecvată pentru material și operațiune.
- Optimizați parametrii de tăiere: Reglați vitezele de avans, vitezele de tăiere și adâncimile de tăiere pentru a optimiza formarea și evacuarea așchiilor.
- Utilizați lubrifiere adecvată: Utilizarea corectă a fluidelor de tăiere poate ajuta la lubrifierea și facilita evacuarea așchiilor.
- Verificați alinierea sculei și a piesei de prelucrat: Asigurați-vă că unealta este aliniată corect cu piesa de prelucrat pentru a preveni problemele legate de așchii.
5. Ruperea sculei:
Problema: Ruperea sculei poate apărea din cauza forței excesive, a configurației incorecte a sculei sau a problemelor legate de material.
Soluţie:
- Optimizați parametrii de tăiere: Reduceți forțele de tăiere prin ajustarea parametrilor precum vitezele de avans, vitezele de tăiere și adâncimile de tăiere.
- Verificați setarea instrumentului: Asigurați-vă că unealta este montată în siguranță în suportul pentru scule și că este aliniată corect.
- Utilizați un material adecvat pentru instrumente: Alegeți materialul de sculă potrivit pentru materialul specific pe care îl prelucrați. De exemplu, sculele din carbură sunt mai bune pentru materiale dure.
- Verificați uzura sculei: Verificați regulat instrumentul pentru semne de uzură și înlocuiți-l înainte de a deveni excesiv de uzat și predispus la rupere.
Abordarea acestor probleme comune de setare a instrumentelor necesită o combinație de instruire adecvată, întreținere regulată și o abordare sistematică a depanării. Capacitatea de a diagnostica și rezolva problemele legate de scule este esențială pentru obținerea unor rezultate de prelucrare eficiente și de înaltă calitate.
În Concluzie
Procesul de instalare și optimizare a sculelor de tăiere cu strung pentru strunjirea CNC este un aspect crucial al prelucrarii, care are un impact semnificativ asupra calității, eficienței și preciziei proceselor de fabricație. O înțelegere profundă a componentelor și funcțiilor sculelor așchietoare, precum și a factorilor implicați în selecția sculelor, este esențială pentru mașiniști și operatorii CNC.
Configurarea corectă a unei scule de tăiere implică o abordare sistematică, de la pregătirea strungului și a piesei de prelucrat până la selectarea suportului corect de sculă, montarea sculei, ajustarea înălțimii sculei și alinierea liniei centrale și configurarea compensării razei sculei și a decalajelor sculei. Fiecare pas joacă un rol esențial în obținerea unor rezultate de prelucrare precise și eficiente.
Optimizarea parametrilor de așchiere, inclusiv vitezele și avansurile, adâncimea de tăiere, fluidele de tăiere și gestionarea duratei de viață a sculei, este un alt aspect critic al strunjirii CNC. Selectând cu atenție parametrii potriviți, mașinii pot crește productivitatea, menține longevitatea sculei și pot îmbunătăți calitatea finisajului suprafeței.
În cele din urmă, posibilitatea de a depana problemele obișnuite de setare a sculei, cum ar fi vibrația sculei, finisarea slabă a suprafeței, inexactitățile dimensionale, problemele de control a așchiilor și ruperea sculei, este esențială pentru menținerea rezultatelor de prelucrare consistente și de înaltă calitate. Identificarea acestor probleme și implementarea soluțiilor adecvate asigură că procesul de prelucrare rămâne neted și eficient.
În general, o înțelegere cuprinzătoare a sculelor de tăiere cu strung și configurarea acestora, combinată cu capacitatea de a optimiza parametrii de tăiere și de a depana problemele, dă putere mașinilor să obțină cele mai bune rezultate în operațiunile de strunjire CNC. Învățarea continuă, formarea și experiența sunt cheie în perfecționarea acestor abilități și pentru asigurarea proceselor de prelucrare de succes.
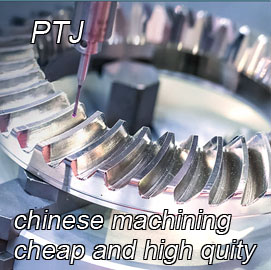
- Prelucrarea cu 5 axe
- Cnc Frezare
- Întoarcere CNC
- Industrii de prelucrare
- Proces de prelucrare
- Tratament de suprafață
- Prelucrarea metalelor
- Prelucrarea materialelor plastice
- Mold Metalurgie Pulbere
- Die Casting
- Galeria pieselor
- Piese metalice auto
- Piese de masina
- Radiator cu LED
- Piese de construcție
- Piese mobile
- Piese medicale
- Parți electronice
- Prelucrare personalizată
- Piese de schimb pentru biciclete
- Prelucrarea aluminiului
- Prelucrarea cu titan
- Prelucrarea oțelului inoxidabil
- Prelucrarea cuprului
- Prelucrarea alamei
- Prelucrare super aliaj
- Prelucrare peek
- Prelucrare UHMW
- Prelucrare unilat
- PA6 Prelucrare
- Prelucrare PPS
- Prelucrarea teflonului
- Prelucrare Inconel
- Prelucrarea oțelului pentru unelte
- Mai mult material