Cum sunt prelucrate piesele de înaltă precizie
2023-09-22
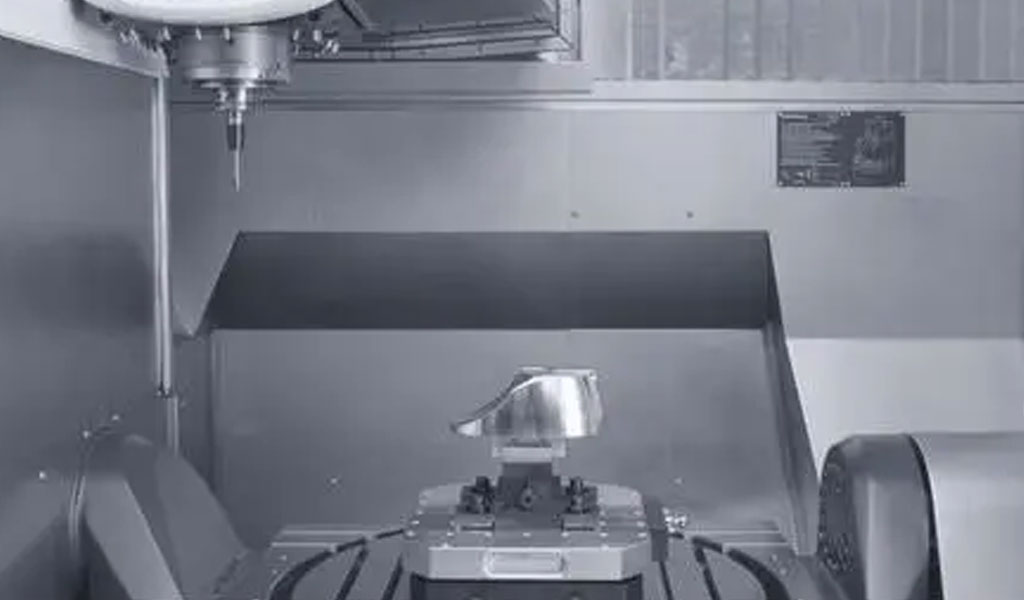
Înțelegerea prelucrării de precizie
Prelucrarea de precizie este o piatră de temelie a producției moderne, responsabilă pentru producerea de componente complexe și precise utilizate într-o gamă largă de industrii. Pentru a înțelege pe deplin semnificația acesteia, haideți să explorăm conceptele de bază ale prelucrării de precizie, rolul său vital în diferite sectoare și călătoria istorică care a condus la starea sa actuală de excelență.A. Ce este prelucrarea de precizie?
Prelucrarea de precizie se referă la un set de procese de fabricație care îndepărtează materialul dintr-o piesă de prelucrat cu un grad ridicat de precizie și control, rezultând componente fin lucrate cu toleranțe strânse. Acest proces transformă materiile prime, cum ar fi metalele, materialele plastice sau ceramica, în piese precise care îndeplinesc specificații stricte. Caracteristicile cheie ale prelucrarii de precizie includ:- Acuratete: Prelucrarea de precizie asigură că produsul final se conformează exact designului dorit, cu abateri minime.
- Toleranțe strânse: Permite producerea de piese cu toleranțe extrem de strânse, ceea ce înseamnă că componentele finite aderă îndeaproape la măsurătorile specificate.
- Finisaj de suprafață superior: Prelucrarea de precizie oferă finisaje excepționale ale suprafețelor, eliminând adesea necesitatea unor procese suplimentare de finisare.
- Geometrii complexe: Poate crea forme, contururi și caracteristici complicate, făcându-l indispensabil în fabricarea componentelor cu design complexe.
- Repetabilitate: Precizie proces de prelucrareAcestea sunt foarte repetabile, asigurând o calitate constantă în mai multe părți.
- Versatilitate: Poate fi aplicat pe o gamă largă de materiale, făcându-l potrivit pentru diverse industrii.
B. Importanța prelucrării de precizie
Prelucrarea de precizie are o importanță imensă în mai multe industrii critice, având impact asupra diferitelor aspecte ale vieții noastre de zi cu zi. Iată câteva motive convingătoare ale importanței sale:- Industrie aerospatiala: În sectorul aerospațial, prelucrarea de precizie este indispensabilă pentru fabricarea de componente care rezistă la condiții extreme. Motoare de avioane, aterizare echipamentul , iar elementele structurale se bazează pe piese prelucrate cu precizie pentru siguranță și performanță.
- Dispozitive medicale: Dispozitivele medicale precum instrumentele chirurgicale, protezele și dispozitivele implantabile necesită prelucrare de precizie pentru biocompatibilitate, acuratețe și siguranța pacientului.
- Sectorul Auto: Piesele prelucrate cu precizie sunt esențiale pentru industria auto pentru a asigura fiabilitatea și eficiența vehiculelor. Componentele precum piesele motorului, sistemele de transmisie și mecanismele de frânare se bazează pe o prelucrare precisă.
- Electronică și semiconductoare: Prelucrarea de precizie este esențială în producția de componente microelectronice și dispozitive semiconductoare, unde toleranțe minuscule sunt imperative pentru funcționalitate.
- Sectorul energetic: Industria energetică se bazează pe prelucrarea de precizie pentru producția de piese critice utilizate în generarea de energie, inclusiv turbine, generatoare și componente de transmisie.
- Fabricarea de scule și matrițe: Prelucrarea de precizie este crucială în fabricarea sculelor și matrițelor, care, la rândul lor, sunt folosite pentru a crea nenumărate alte produse.
- Consumer Electronics: Producția de smartphone-uri, laptop-uri și alte produse electronice de larg consum beneficiază de prelucrarea de precizie pentru a asigura un design elegant și o funcționalitate optimă.
- Cercetare și dezvoltare: Cercetătorii și oamenii de știință depind de componente prelucrate cu precizie pentru experimente, prototipuri și echipamente de laborator.
C. Perspectivă istorică
Călătoria prelucrării de precizie are originea în civilizațiile antice, unde artizanii pricepuți foloseau unelte rudimentare pentru a modela materialele. Cu toate acestea, precizia obținută în acele vremuri a fost limitată în comparație cu standardele contemporane.- Prelucrare de precizie timpurie: Revoluția industrială din secolele al XVIII-lea și al XIX-lea a marcat o perioadă esențială în dezvoltarea prelucrării de precizie. Invenția mașinilor-unelte, cum ar fi strungurile și mașinile de frezat, a revoluționat producția, permițând o mai mare acuratețe și consistență.
- Al doilea război mondial: Prelucrarea de precizie a jucat un rol esențial în al Doilea Război Mondial, deoarece a fost esențială pentru producerea de echipamente militare cu precizia și uniformitatea necesare. Această epocă a fost martoră la progrese în tehnicile de prelucrare și la apariția de noi materiale.
- Progrese postbelice: Perioada postbelică a cunoscut o creștere a inovațiilor tehnologice, inclusiv utilizarea mașinilor cu control numeric computerizat (CNC). Prelucrare CNC a permis operațiuni automate și extrem de precise, inaugurând o nouă eră a producției.
- Era digitală: Integrarea computerelor și a software-ului în procesele de prelucrare a ridicat și mai mult prelucrarea de precizie. Mașinile moderne CNC pot executa operațiuni complexe cu o precizie de neegalat, făcându-le indispensabile în peisajul producției de astăzi.
Materialele și semnificația lor
Materialele sunt fundamentul prelucrării de precizie, iar selecția materialului potrivit joacă un rol esențial în producția de piese de înaltă precizie. În această secțiune, vom explora importanța selectării materialelor adecvate, vom înțelege semnificația proprietăților materialelor și vom explora diferiții factori care afectează prelucrabilitatea.A. Selectarea materialelor
Alegerea materialelor în prelucrarea de precizie este o decizie critică care are un impact direct asupra performanței, durabilității și funcționalității produsului final. Producătorii trebuie să ia în considerare mai mulți factori atunci când selectează materiale:- Adecvarea materialului: Materialul trebuie să fie adecvat pentru aplicarea prevăzută. Diferitele industrii și aplicații au cerințe diferite, cum ar fi rezistența la temperatură, rezistența la coroziune și conductivitatea electrică.
- Proprietăți mecanice: Proprietățile mecanice precum rezistența la tracțiune, duritatea și ductilitatea sunt cruciale. De exemplu, în domeniul aerospațial, materialele cu rezistență mare la tracțiune sunt preferate pentru componentele structurale.
- Proprietati termice: Unele aplicații necesită materiale cu conductivitate termică excelentă sau rezistență la temperaturi ridicate. Acest lucru este deosebit de important în industrii precum generarea de energie și electronica.
- Rezistența la coroziune: În mediile în care coroziunea este o problemă, sunt preferate materialele cu rezistență ridicată la coroziune, cum ar fi oțelul inoxidabil sau titanul.
- Considerații privind greutatea: Industrii precum cel auto și cel aerospațial acordă prioritate materialelor ușoare precum aluminiul sau compozitele din fibră de carbon pentru a reduce consumul de combustibil și a îmbunătăți performanța.
- Constrângeri de cost: Costul este un factor semnificativ în selecția materialelor. Materialele de înaltă performanță pot fi costisitoare, așa că producătorii trebuie să găsească un echilibru între performanță și rentabilitate.
- Respectarea reglementărilor: În industrii precum asistența medicală, materialele trebuie să îndeplinească standarde de reglementare stricte pentru biocompatibilitate și siguranță.
- Disponibilitate: Disponibilitatea materialelor și sursele acestora afectează, de asemenea, selecția. Unele aliaje sau compozite specializate pot avea o disponibilitate limitată.
B. Proprietăţile materialelor
Înțelegerea proprietăților materialelor este crucială pentru prelucrarea de precizie. Iată câteva proprietăți cheie ale materialului și semnificația lor:- Forța de tracțiune: Rezistența la tracțiune măsoară capacitatea unui material de a rezista la o forță de tracțiune fără a se rupe. Este esențială pentru componentele structurale și piesele supuse solicitărilor mecanice.
- Duritate: Duritatea indică rezistența unui material la deformare și uzură. Materialele dure sunt potrivite pentru sculele de tăiere, în timp ce materialele mai moi pot fi preferate pentru anumite aplicații, cum ar fi garniturile.
- Ductilitate: Ductilitatea se referă la capacitatea unui material de a se deforma fără a se rupe atunci când este supus unei solicitări de tracțiune. Materialele ductile sunt mai ușor de modelat, dar pot să nu fie potrivite pentru aplicații care necesită rigiditate.
- Conductivitate termică: Materialele cu conductivitate termică ridicată disipează eficient căldura. Această proprietate este vitală în aplicațiile în care controlul temperaturii este critic.
- Conductivitate electrică: Conductivitatea electrică este esențială în electronică și componentele electrice, unde materialele trebuie să faciliteze fluxul de electricitate.
- Proprietăți magnetice: Proprietățile magnetice sunt semnificative în industrii precum electromagnetică și electronică, unde materialele pot fi feromagnetice sau nemagnetice.
- Rezistență chimică: Materialele trebuie să reziste la coroziunea chimică în medii în care sunt expuse la acizi, baze sau alte substanțe corozive.
C. Factori de prelucrabilitate
Prelucrabilitatea se referă la ușurința cu care un material poate fi prelucrat, tăiat sau modelat. Este influențată de diverși factori, printre care:- Duritate materială: Materialele mai moi sunt în general mai ușor de prelucrat, în timp ce materialele mai dure pot necesita instrumente și tehnici specializate.
- Formarea așchiilor: Formarea și evacuarea așchiilor în timpul prelucrării afectează eficiența procesului și finisarea suprafeței.
- Uzura sculei: Materialele diferite pot cauza diferite grade de uzură a sculei, influențând viteza de prelucrare și costul.
- Lichid de răcire și lubrifiere: Lichidul de răcire și lubrifierea adecvate sunt esențiale pentru a reduce frecarea, căldura și uzura sculelor în timpul prelucrării.
- Viteza de tăiere: Viteza cu care scula de tăiere se deplasează prin material afectează atât productivitatea, cât și calitatea suprafeței prelucrate.
- Materialul sculei: Alegerea materialului sculei de tăiere, cum ar fi carbură sau oțel rapid, depinde de materialul prelucrat.
- Parametrii de tăiere: Ajustarea parametrilor de tăiere, cum ar fi viteza de avans și adâncimea de tăiere, poate optimiza procesul de prelucrare pentru anumite materiale.
Masini-unelte pentru prelucrare de precizie
Mașinile-unelte reprezintă inima prelucrării de precizie, permițând transformarea materiilor prime în piese de înaltă precizie. În această secțiune, vom explora patru tipuri cheie de mașini-unelte utilizate în prelucrarea de precizie: centre de prelucrare CNC, mașini de strunjire, mașini de șlefuit și EDM (prelucrare cu descărcare electrică). Fiecare dintre aceste mașini joacă un rol unic în producția de componente precise.A. Centre de prelucrare CNC
Centrele de prelucrare CNC (Computer Numerical Control) sunt versatile și utilizate pe scară largă în prelucrarea de precizie. Sunt sisteme automate care controlează mișcarea sculelor de tăiere și a pieselor de prelucrat cu o precizie excepțională. Iată o prezentare generală a centrelor de prelucrare CNC și a semnificației acestora:- Versatilitate: Centrele de prelucrare CNC pot efectua diverse operațiuni de prelucrare, inclusiv frezare, găurire și filetare. Această versatilitate permite producerea de piese complexe cu caracteristici multiple.
- Precizie ridicata: Controlul computerizat al mașinilor CNC asigură poziționarea precisă a sculei și rezultate consistente, făcându-le ideale pentru piese cu toleranțe strânse.
- Automatizare: Centrele de prelucrare CNC pot funcționa continuu, cu intervenție umană minimă. Această automatizare crește eficiența și reduce riscul de erori.
- Geometrii complexe: Excelează în prelucrarea formelor și contururilor complicate, făcându-le potrivite pentru industrii precum aerospațial, unde componentele complexe sunt comune.
- Rezultate repetabile: Mașinile CNC oferă o repetabilitate excelentă, asigurându-se că fiecare piesă produsă se potrivește cu specificațiile exacte ale designului.
- Timp de instalare redus: Centrele de prelucrare CNC pot fi programate pentru a comuta rapid între diferite sarcini, minimizând timpii de configurare și crescând eficiența producției.
B. Mașini de strunjire
Mașinile de strunjire sunt folosite pentru a crea piese cilindrice prin rotirea unei piese de prelucrat, în timp ce o unealtă de tăiere îndepărtează materialul de pe suprafața sa exterioară. Sunt esențiale pentru producere axs, pini și alte componente cu simetrie de rotație. Punctele cheie despre mașinile de strunjire includ:- Piese cilindrice: Mașinile de strunjire sunt specializate în producerea de componente cilindrice sau tubulare, inclusiv cele cu filete sau caneluri complicate.
- Viteze mari: Funcționează la viteze mari, făcându-le potrivite pentru piesele care necesită o finisare netedă și precisă.
- Operare pe o singură axă: Majoritatea mașinilor de strunjire sunt cu o singură axă, concentrându-se pe modelarea suprafeței exterioare a piesei de prelucrat.
- Eficient pentru producția de masă: Strunjirea este foarte eficientă pentru piese de producție în masă cu risipă minimă de material.
- Mașini de strung: Mașinile de strung manuale și controlate CNC sunt mașini de strunjire utilizate în mod obișnuit, oferind o gamă largă de capabilități.
C. Masini de slefuit
Mașinile de șlefuit sunt proiectate pentru finisarea de precizie a suprafețelor și modelarea materialelor dure sau abrazive. Sunt esențiale pentru obținerea unor toleranțe extrem de strânse și finisaje superioare ale suprafeței. Iată de ce mașinile de șlefuit sunt importante:- Precizie la nivel de microni: Mașinile de șlefuit pot atinge o precizie la nivel de microni, făcându-le esențiale pentru aplicațiile care necesită cel mai înalt nivel de precizie.
- Îndepărtarea materialului: Îndepărtează materialul prin abraziune, permițând corectarea imperfecțiunilor suprafeței și obținând o netezime excepțională.
- Slefuire cu scule și tăietori: Pe lângă șlefuirea suprafețelor, există mașini de șlefuit specializate pentru ascuțirea sculelor de tăiere și producerea de profile precise.
- Varietate de metode de măcinare: Diferite tipuri de mașini de șlefuit, inclusiv polizoare de suprafață, polizoare cilindrice și polizoare fără centru, răspund diferitelor nevoi de prelucrare.
- Materiale întărite: Slefuirea este potrivită în special pentru materiale întărite, cum ar fi oțelul de scule și ceramica, unde metodele tradiționale de prelucrare pot fi ineficiente.
D. EDM (prelucrare cu descărcare electrică)
EDM, sau Prelucrarea cu descărcare electrică, este un proces de prelucrare netradițional care utilizează descărcări electrice pentru a modela materialele. Este ideal pentru crearea de piese complicate și delicate în care uneltele tradiționale de tăiere pot provoca daune. Aspectele cheie ale EDM includ:- Fără contact fizic: EDM nu implică contact fizic direct între unealtă și piesa de prelucrat, minimizând riscul de uzură a sculei și deteriorarea materialelor fragile.
- Precizie ridicata: Poate obține o precizie ridicată și o calitate a finisajului suprafeței, chiar și cu materiale excepțional de dure.
- Wire EDM și Sinker EDM: Există două tipuri principale de mașini EDM: tăierea sârmei EDM, care folosește un electrod de sârmă, și EDM sinker, care utilizează un electrod în formă.
- Forme complexe: EDM poate produce forme complexe, cum ar fi matrițe și matrițe, cu detalii complicate și caracteristici fine.
- Zona afectată de căldură: Deoarece EDM nu generează căldură la piesa de prelucrat, este potrivit pentru materiale sensibile la căldură precum aliajele aerospațiale.
- Proces lent: EDM este relativ lentă în comparație cu alte metode de prelucrare, ceea ce o face cel mai potrivită pentru lucrări de înaltă precizie și în cantitate mică.
Scule de tăiere și scule
Uneltele de tăiere sunt în fruntea prelucrării de precizie, servind drept instrumente care modelează și transformă materiile prime în piese de înaltă precizie. În această secțiune, vom explora diferitele tipuri de scule de tăiere, importanța acoperirii sculelor și factorii care afectează durata de viață și uzura sculei.A. Tipuri de scule de tăiere
Prelucrarea de precizie se bazează pe o gamă diversă de scule de tăiere, fiecare proiectată pentru sarcini și materiale specifice. Alegerea sculei de tăiere influențează foarte mult eficiența și precizia procesului de prelucrare. Iată câteva tipuri comune de instrumente de tăiere:- Mori de capat: Frezele sunt unelte versatile utilizate pentru operațiunile de frezare. Au mai multe muchii de tăiere și pot îndepărta materialul din piesa de prelucrat în diferite moduri, inclusiv confruntare, conturare și crestare.
- Burghie: Burghiile sunt concepute pentru a crea gauri in piesele de prelucrat. Ele vin sub diferite forme, inclusiv burghie elicoidale, burghie de centrare și burghie indexabile.
- Întoarcerea inserțiilor: Acestea sunt folosite la mașinile de strunjire pentru modelarea pieselor cilindrice. Inserțiile de strunjire sunt disponibile într-o varietate de forme și materiale pentru a se potrivi diferitelor aplicații.
- Freze: Frezele vin în diferite forme, cum ar fi freze cu bile, freze cu bile și freze cu fante și sunt utilizate la mașinile de frezat pentru a crea diferite caracteristici pe piesa de prelucrat.
- Alezori: Alezoarele sunt folosite pentru finisarea și dimensionarea găurilor găurite anterior la dimensiuni precise. Acestea asigură suprafețe netede și precise ale orificiilor.
- Taps and Dies: Aceste scule de tăiere sunt utilizate pentru operațiunile de filetare. Tapsele creează fire interne, în timp ce matrițele creează fire externe.
- Discuri abrazive: Molele abrazive sunt instrumente abrazive utilizate pentru șlefuirea de precizie a suprafețelor. Sunt disponibile în diferite materiale abrazive și dimensiuni de granulație.
- Broșuri: Broșele sunt unelte specializate utilizate pentru tăierea formelor și profilelor interne și externe, cum ar fi canalele și canelurile.
- Lamare și lamă: Aceste instrumente sunt folosite pentru a crea adâncituri sau teșituri în jurul găurilor pt element de fixares.
- Baruri plictisitoare: Barele de foraj sunt folosite în operațiunile de foraj pentru a mări cu precizie găurile existente.
B. Acoperiri pentru scule
Acoperirile pentru scule sunt straturi subțiri de material aplicate pe sculele de tăiere pentru a le îmbunătăți performanța și durabilitatea. Aceste acoperiri oferă mai multe avantaje:- Frecare redusă: Acoperirile precum nitrura de titan (TiN) și carbonitrura de titan (TiCN) reduc frecarea dintre sculă și piesa de prelucrat, ceea ce duce la o tăiere mai lină și o durată de viață mai lungă a sculei.
- Duritate sporită: Acoperirile cresc duritatea suprafeței sculei, făcând-o mai rezistentă la uzură și prelungind durata de viață a sculei.
- Rezistență la căldură îmbunătățită: Acoperirile pot rezista la temperaturi ridicate generate în timpul prelucrării, reducând uzura sculelor cauzată de căldură și crescând vitezele de tăiere.
- Proprietăți anti-acumulare: Unele acoperiri au proprietati anti-aderenta, impiedicand acumularea de material pe marginile de taiere ale sculei.
- Lubricitate crescută: Uneltele acoperite au o lubrifiere îmbunătățită, reducând nevoia de lichid de răcire excesiv și îmbunătățind evacuarea așchiilor.
C. Durata de viață și uzura sculei
Înțelegerea duratei de viață a sculei și a uzurii este crucială pentru optimizarea proceselor de prelucrare și minimizarea costurilor de producție. Durata de viață a sculei se referă la durata în care o unealtă de tăiere rămâne eficientă înainte de a necesita înlocuire sau recondiționare. Mai mulți factori influențează durata de viață și uzura sculei:- Viteza de tăiere: Vitezele de așchiere mai mari pot duce la o uzură crescută a sculei din cauza temperaturilor mai ridicate generate în timpul prelucrării. Selectarea corectă a vitezelor de așchiere este esențială pentru a echilibra durata de viață a sculei și productivitatea.
- Rata de hranire: Rata cu care scula de tăiere avansează în piesa de prelucrat afectează uzura sculei. Vitezele de avans ridicate pot accelera uzura, în timp ce vitezele de avans mai mici pot prelungi durata de viață a sculei.
- Adâncimea tăieturii: Adâncimea de tăiere influențează cantitatea de material îndepărtat pe trecere. Tăieturile mai adânci pot crește uzura sculei, astfel încât optimizarea adâncimii este esențială.
- Duritate materială: Tăierea materialelor dure poate accelera uzura sculei. Pentru prelucrarea eficientă a materialelor dure se folosesc scule și acoperiri specializate.
- Lichid de răcire și lubrifiere: Lichidul de răcire și lubrifierea adecvate ajută la disiparea căldurii și la reducerea frecării, prelungind durata de viață a sculei.
- Materialul sculei: Materialul din care este realizată unealta de tăiere îi afectează rezistența la uzură. Materiale precum carbura și ceramica oferă o rezistență excelentă la uzură.
- Geometria sculei: Geometria sculei de tăiere, inclusiv unghiul de greblare, unghiul de relief și designul ruptorului de așchii, joacă un rol semnificativ în modelele de uzură.
- Materialul piesei de prelucrat: Tipul de material prelucrat afectează uzura sculei. Materialele abrazive pot duce la uzura mai rapidă a sculei.
Procese de prelucrare de precizie
Procesele de prelucrare de precizie sunt metodele prin care materiile prime sunt transformate in piese de inalta precizie, cu tolerante stranse si finisaje exceptionale ale suprafetelor. În această secțiune, vom explora cinci procese cheie de prelucrare de precizie: strunjire, frezare, găurire, șlefuire și prelucrare cu descărcare electrică (EDM). Fiecare dintre aceste procese servește unui scop unic și este utilizat pe baza cerințelor specifice ale piesei de prelucrat.A. Întorcându-se
Strunjirea este un proces de prelucrare utilizat în principal pentru modelarea pieselor cilindrice. Aceasta implică rotirea unei piese de prelucrat în timp ce o unealtă de tăiere cu un singur punct îndepărtează materialul de pe suprafața exterioară. Iată care sunt aspectele cheie ale strunjirii:- Piese cilindrice: Strunjirea este ideală pentru producerea de componente cilindrice, cum ar fi arbori, știfturi și manșoane.
- Simetria rotațională: Este potrivit pentru piese care necesită simetrie de rotație, deoarece piesa de prelucrat se rotește pe un strung în timp ce unealta de tăiere o modelează.
- Operații diverse: strunjirea poate efectua diverse operații, inclusiv fațare, strunjire (reducerea diametrului), strunjire conică și filetare.
- Tăiere într-un singur punct: O singură unealtă de tăiere îndepărtează materialul într-o mișcare continuă, rezultând o îndepărtare eficientă a materialului.
- Mașini de strung: Atât mașinile de strung manuale, cât și cele controlate de CNC sunt utilizate în mod obișnuit pentru operațiunile de strunjire.
B. Frezare
Frezarea este un proces de prelucrare de precizie versatil care folosește unelte de tăiere în mai multe puncte pentru a îndepărta materialul dintr-o piesă de prelucrat. Este potrivit pentru crearea unei game largi de forme și caracteristici. Aspectele cheie ale măcinarii includ:- Versatilitate: Frezarea poate produce suprafețe plane, fante, buzunare și contururi complexe. Este folosit atât pentru prelucrarea 2D, cât și pentru prelucrarea 3D.
- Tăiere în mai multe puncte: Mai multe muchii de tăiere de pe unealta interacționează cu piesa de prelucrat simultan, permițând îndepărtarea eficientă a materialului.
- Tipuri de frezare: Frezarea poate fi efectuată folosind diferite tipuri de freze, inclusiv freze cu cap, freze frontale și mori cu bile.
- Centre de prelucrare CNC: Mașinile de frezat controlate de CNC oferă un control precis asupra mișcării sculei și sunt utilizate pe scară largă în prelucrarea modernă.
- Viteze mari: Frezarea poate fi efectuată la viteze mari, permițând o producție eficientă.
C. Foraj
Găurirea este un proces de prelucrare de precizie utilizat pentru a crea găuri în piesele de prelucrat. Este o operațiune fundamentală în diverse industrii. Aspectele cheie ale forajului includ:- Crearea gaurii: Mașinile de găurit folosesc unelte specializate numite burghie pentru a îndepărta materialul și pentru a crea găuri cu diametre specifice.
- Tipuri de burghie: Sunt disponibile diferite tipuri de burghie, inclusiv burghie elicoidale, burghie de centrare și burghie indexabile, fiecare proiectat pentru aplicații specifice.
- Acuratete: Poziționarea și alinierea precisă sunt esențiale în găurire pentru a asigura că găurile sunt create cu precizie.
- Viteza și viteza de avans: Parametrii de găurire, cum ar fi viteza de rotație și viteza de avans, sunt critici pentru obținerea dimensiunilor dorite ale găurilor.
- Lichid de răcire și lubrifiere: Se utilizează lichid de răcire și lubrifiere adecvate pentru a disipa căldura și pentru a reduce frecarea în timpul forajului.
D. Măcinarea
Slefuirea este un proces de prelucrare de precizie care folosește roți abrazive pentru a îndepărta materialul și pentru a obține toleranțe extrem de strânse și finisaje ale suprafeței. Aspectele cheie ale măcinarii includ:- Precizie excepțională: Măcinarea poate atinge o precizie la nivel de microni, făcându-l ideal pentru aplicații care necesită cea mai mare precizie.
- Finisarea de suprafață: Produce finisaje superioare ale suprafeței, eliminând adesea nevoia unor procese suplimentare de finisare.
- materiale: Slefuirea este potrivită pentru materiale dure și abrazive, inclusiv oțel întărit, ceramică și carburi.
- Varietate de metode de măcinare: Diferite tipuri de mașini de șlefuit, cum ar fi polizoarele de suprafață, polizoarele cilindrice și polizoarele fără centru, răspund diferitelor nevoi de prelucrare.
- Lichid de răcire: Lichidul de răcire adecvat este esențial în șlefuire pentru a preveni supraîncălzirea și pentru a menține integritatea roții.
E. Prelucrare cu descărcare electrică (EDM)
EDM, sau Prelucrarea cu descărcare electrică, este un proces de prelucrare de precizie netradițional care utilizează descărcări electrice pentru a îndepărta materialul. Este deosebit de potrivit pentru prelucrarea formelor complexe și complicate, precum și a materialelor dure și rezistente la căldură. Aspectele cheie ale EDM includ:- Prelucrare fără contact: EDM nu implică contact direct între unealtă și piesa de prelucrat, reducând riscul de uzură și deteriorare a sculei.
- Precizie ridicata: EDM poate atinge o precizie ridicată, făcându-l potrivit pentru aplicații în care toleranțe strânse sunt esențiale.
- Forme complexe: Excelează în prelucrarea formelor complexe, matrițelor, matrițelor și componentelor cu detalii fine.
- Wire EDM și Sinker EDM: Există două tipuri principale de mașini EDM: electroeroziune cu sârmă, care folosește un electrod cu sârmă, și EDM cu plată, care utilizează un electrod în formă.
- Proces lent: EDM este relativ lentă în comparație cu alte metode de prelucrare, ceea ce o face cel mai potrivită pentru lucrări de înaltă precizie și în cantitate mică.
Toleranțe și control al calității
Prelucrarea de precizie necesită o atenție meticuloasă la detalii și un angajament riguros față de controlul calității pentru a se asigura că piesele respectă standardele specificate. În această secțiune, vom explora trei aspecte critice ale controlului calității în prelucrarea de precizie: Dimensionarea și toleranța geometrică (GD&T), Controlul statistic al procesului (SPC) și Asigurarea calității.A. Dimensionarea și toleranța geometrică (GD&T)
Dimensionarea și toleranța geometrică, adesea abreviată ca GD&T, este un sistem utilizat pentru a defini și comunica variațiile permise de dimensiune, formă, orientare și locație a caracteristicilor unei piese. GD&T este vital în prelucrarea de precizie din următoarele motive:- Comunicare precisa: GD&T oferă un limbaj standardizat pentru ingineri, designeri și mașiniști pentru a comunica cu acuratețe intenția de proiectare și cerințele dimensionale.
- Clarificarea toleranței: Ajută la definirea variației acceptabile în dimensiunile critice, asigurând că toate părțile interesate înțeleg abaterile permise.
- Calitate îmbunătățită: GD&T promovează calitatea îmbunătățită prin reducerea ambiguității în specificațiile de proiectare, minimizând riscul erorilor în timpul prelucrării.
- Eficiența costurilor: Specificațiile GD&T clare pot duce la costuri de producție reduse, deoarece piesele sunt mai puțin probabil să fie casate sau să necesite relucrare din cauza neînțelegerii sau interpretării greșite.
- Geometrie complexă: Este deosebit de util pentru piese cu geometrii complexe, asigurându-se că toate caracteristicile sunt fabricate conform specificațiilor dorite.
B. Controlul statistic al procesului (SPC)
Controlul statistic al procesului (SPC) este o metodologie de control al calității care utilizează tehnici statistice pentru a monitoriza și controla procesul de prelucrare. SPC este esențial în prelucrarea de precizie din următoarele motive:- Monitorizarea proceselor: SPC ajută la monitorizarea proceselor de prelucrare în timp real, identificând variațiile sau abaterile de la parametrii doriti.
- Detectarea timpurie a problemelor: Prin monitorizarea continuă a procesului, SPC permite detectarea timpurie a problemelor care ar putea duce la piese în afara specificațiilor, reducând pierderile și reprelucrarea.
- Luare a deciziilor bazată pe date: SPC se bazează pe date și analize statistice pentru a lua decizii informate cu privire la ajustările procesului, asigurându-se că procesul de prelucrare rămâne în limite acceptabile.
- Consistență îmbunătățită: SPC promovează consistența procesului și reduce probabilitatea de a produce piese neconforme.
- Reducerea deșeurilor și a reluării: Prin identificarea și abordarea rapidă a variațiilor de proces, SPC reduce la minimum producția de piese defecte, reducând costurile de deșeuri și reprelucrare.
C. Asigurarea calității în prelucrarea de precizie
Asigurarea calității în prelucrarea de precizie cuprinde o abordare cuprinzătoare pentru a se asigura că piesele fabricate îndeplinesc sau depășesc standardele de calitate specificate. Acesta implică diverse elemente, printre care:- Documentarea procesului: Documentația detaliată a proceselor de prelucrare, inclusiv procedurile standard de operare (SOP) și instrucțiunile de lucru, asigură că fiecare pas este efectuat în mod consecvent.
- Inspecție și Măsurare: Inspecția și măsurarea riguroase folosind instrumente de precizie și tehnici de metrologie verifică dacă piesele sunt conforme cu toleranțele și standardele de calitate specificate.
- Calibrarea: Calibrarea regulată a echipamentelor de prelucrare și a instrumentelor de măsurare este esențială pentru a menține acuratețea și trasabilitatea.
- Verificarea materialului: Verificarea proprietăților, compoziției și calității materialului este esențială pentru a se asigura că materialul utilizat îndeplinește cerințele de proiectare.
- Formarea angajaților: Programele de formare și dezvoltare a abilităților pentru mașiniști și personalul de control al calității asigură că aceștia sunt competenți în rolurile și responsabilitățile lor.
- Analiza cauzelor fundamentale: Când sunt identificate părți neconforme, se efectuează o analiză a cauzei principale pentru a determina sursa problemei și pentru a implementa acțiuni corective.
- Îmbunătățirea continuă: O cultură a îmbunătățirii continue încurajează inovația și generează îmbunătățiri continue în procesele de prelucrare și procedurile de control al calității.
- Clienți Feedback: Colectarea și analizarea feedback-ului clienților ajută la identificarea zonelor de îmbunătățire și aliniază procesele de prelucrare cu așteptările clienților.
Concluzie
A. Arta și știința prelucrării de precizie
Prelucrarea de precizie se află la intersecția artei și științei, unde creativitatea, priceperea și inovația converg pentru a produce piese de înaltă precizie care conduc industriile și modelează lumea modernă. Este atât o formă de artă, care necesită măiestria și expertiza mașinilor care transformă materiile prime în lucrări de excelență inginerească, cât și o știință care se bazează pe tehnologie de ultimă oră, știința materialelor și procese avansate pentru a obține o precizie de neegalat. Călătoria prelucrării de precizie ne duce prin înțelegerea materialelor și a proprietăților acestora, stăpânirea sculelor și mașinilor așchietoare și controlul meticulos al proceselor și toleranțelor. Acesta cuprinde limbajul dimensionării geometrice și al toleranței, vigilența controlului statistic al procesului și angajamentul față de asigurarea calității. Prelucrarea de precizie joacă un rol esențial în diverse industrii, de la industria aerospațială și auto până la dispozitive medicale și electronice, modelând totul, de la motoarele de avioane la articulații artificiale și microcipuri. Permite crearea de componente care funcționează cu o acuratețe și fiabilitate de neegalat, depășind adesea limitele a ceea ce este posibil.B. Gânduri finale
Pe măsură ce încheiem această explorare a prelucrării de precizie, este clar că acest domeniu nu este doar despre crearea de piese; este vorba despre crearea de posibilităţi. Căutarea preciziei conduce la inovație, depășind limitele a ceea ce poate fi realizat. Fie că este vorba de măiestria delicată necesară pentru a crea roțile complicate ale unui ceas sau de tehnologia avansată necesară pentru fabricarea componentelor aerospațiale complexe, prelucrarea de precizie este în centrul tuturor. Viitorul prelucrării de precizie este plin de promisiuni. Progresele în domeniul științei materialelor, automatizării și tehnologiilor digitale continuă să remodeleze peisajul. Miniaturizarea, imprimarea 3D și practicile de producție durabilă devin din ce în ce mai importante, aducând noi orizonturi pentru industrie. Într-o lume în care precizia contează mai mult ca niciodată, prelucrarea de precizie rămâne un pilon indispensabil al ingineriei moderne. Este o dovadă a ingeniozității umane și a urmăririi noastre neînduplecabile de excelență în fiecare aspect al producției. Pe măsură ce cererea pentru o precizie mai mare și componente mai complicate crește, prelucrarea de precizie va continua să evolueze, răspunzând provocărilor de mâine cu aceeași dedicare și precizie care au definit-o de secole.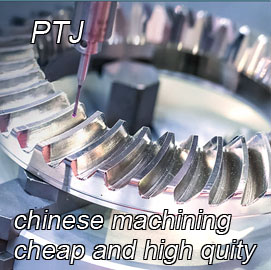
Serviciile noastre
- Prelucrarea cu 5 axe
- Cnc Frezare
- Întoarcere CNC
- Industrii de prelucrare
- Proces de prelucrare
- Tratament de suprafață
- Prelucrarea metalelor
- Prelucrarea materialelor plastice
- Mold Metalurgie Pulbere
- Die Casting
- Galeria pieselor
Studii De Caz
- Piese metalice auto
- Piese de masina
- Radiator cu LED
- Piese de construcție
- Piese mobile
- Piese medicale
- Parți electronice
- Prelucrare personalizată
- Piese de schimb pentru biciclete
Lista de materiale
- Prelucrarea aluminiului
- Prelucrarea cu titan
- Prelucrarea oțelului inoxidabil
- Prelucrarea cuprului
- Prelucrarea alamei
- Prelucrare super aliaj
- Prelucrare peek
- Prelucrare UHMW
- Prelucrare unilat
- PA6 Prelucrare
- Prelucrare PPS
- Prelucrarea teflonului
- Prelucrare Inconel
- Prelucrarea oțelului pentru unelte
- Mai mult material
Galeria pieselor